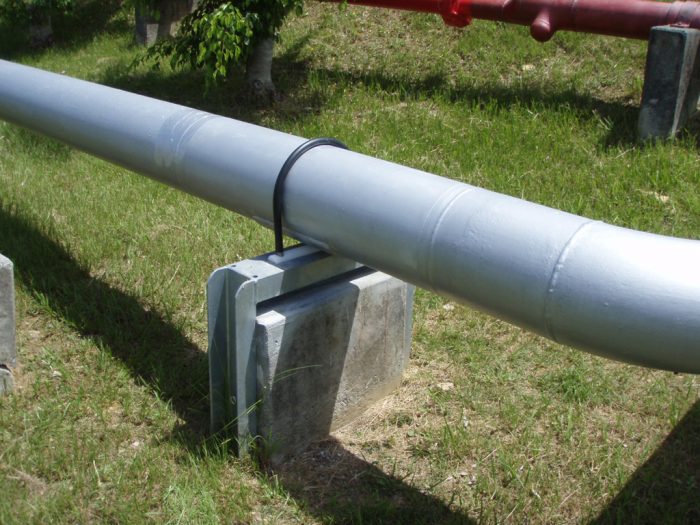
Corrosion occurring at pipe supports is one of the biggest causes of pipe failure in Australia.
If this problem isn’t addressed quickly, there is a risk that entire sections of the pipe will fail.
This can be a particularly big problem for beam supports, saddle supports and pipe shoes at refineries and terminals.
A myth in the pipeline industry is that corrosion at pipe supports is due to the abrasive metal to metal contact between the pipe and the support.
When in fact, crevices can be created between the pipe and its support, allowing water to be trapped in them. This trapped water is then in constant contact with the pipe’s coating for a long period of time and this immersion weakens the coating’s effectiveness, especially if the coating’s specifications were only for intermittent immersion protection.
With the coating then not providing protection from the outside environment, corrosion occurs, which can lead to premature pipe failure. For pipelines at Australian oil and gas refineries and terminals, not only are repairs or replacements a costly and time-consuming process, but pipe failure can have extreme safety and environmental consequences.
The design of standard pipe supports often makes it difficult to undertake inspections, which is the only reliable way to identify crevice corrosion. The best solution to this problem is to eliminate crevices from occuring in the first place.
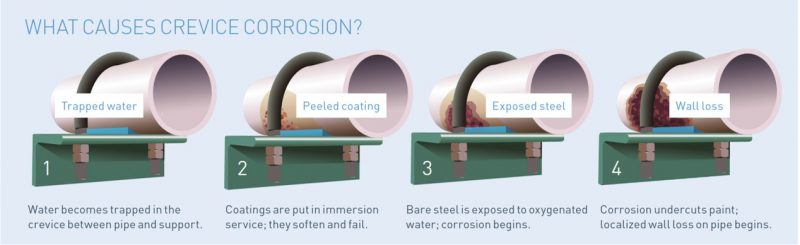
David Anderson, Sales and Marketing Manager at Universal Corrosion Coatings (UCC), said there are a few things companies need to keep in mind in order to stop crevices from being created.
“Pipeline installations need to implement pipe supports that minimise the contact between the pipe and the support while also allowing for easy maintenance and withstanding any temperatures or harsh environments they are subject to,” Mr Anderson said.
UCC is an Australian company that provides solutions to corrosion and material degradation issues in water and oil and gas pipelines, and the marine and civil infrastructure sectors.
UCC is the exclusive distributor of Deepwater Corrosion Services’ Nu-Bolt and I-Rod pipe support for Australia, New Zealand and Papua New Guinea. Deepwater Corrosion Services created the Nu-Bolt and I-Rod pipe support and specifically designed it to combat crevice corrosion. The Nu-bolt contains the I-Rod, a high-strength thermoplastic rod in a half round shape with a modified pipe U-Bolt.
Its half round configuration creates a fixed distance between the pipe and support so water won’t accumulate in between. The standoff insulates electrically and improves maintainability and inspectability.
There are also a range of corrosion-resistant treatments that can be applied if it is operating in a highly corrosive environment. For the vast majority of applications, the standard I-Rod Thermoplastic is the best choice as it has good quality compressive strength and low creep but for temperatures above 180°F, I-Rod HT or PEEK can be substituted.
For further protection, UCC also offers the I-Rod Clip to eliminate crevice corrosion at saddle clamp supports, grinnell clamps and pipe shoes. This works by being placed on the inside diameter of the support, providing a low-profile standoff.
“The Nu-Bolt and I-Rod pipe support is producing major benefits onshore in the midstream and downstream sectors across the US and Europe. If Australian operations are experiencing pipe damage and failures due to crevice corrosion, it’s crucial that crevices are eliminated right at the start,” Mr Anderson said.
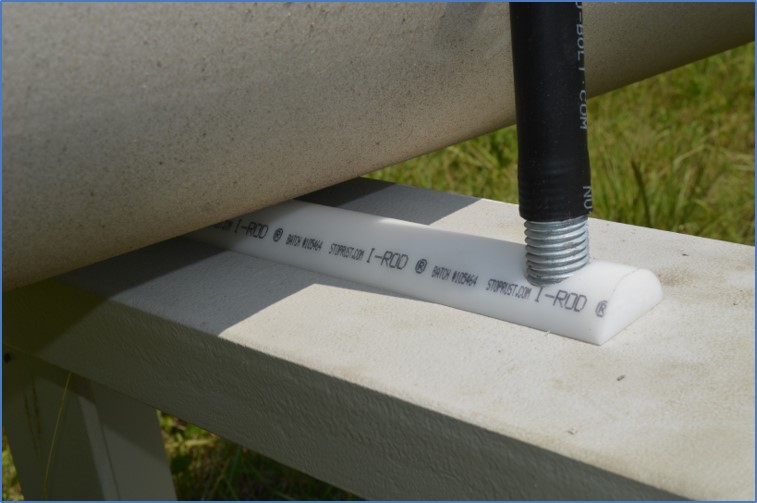